In the dynamic landscape of modern manufacturing, businesses are leveraging advanced technologies to enhance efficiency, streamline operations, and gain a competitive edge. Manufacturing Enterprise Resource Planning (ERP) software emerges as a pivotal solution, seamlessly integrating various facets of production and business processes into a unified system. This article delves into the realm of Manufacturing ERP Software, exploring its significance, key features, benefits, and the transformative impact it brings to the manufacturing sector.
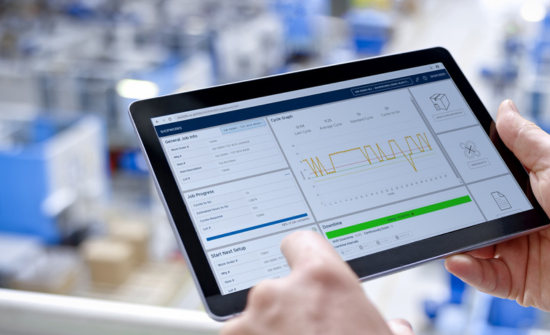
Understanding Manufacturing ERP Software
Manufacturing ERP Software is a comprehensive solution designed to orchestrate and optimize a range of business processes within the manufacturing environment. It goes beyond traditional Enterprise Resource Planning by addressing the unique challenges and intricacies of the manufacturing industry. The primary goal is to integrate core business functions, providing real-time visibility and control over operations.
Key Features of Manufacturing ERP Software
- Production Planning and Scheduling
- Manufacturing ERP systems enable detailed production planning, considering factors like resource availability, demand forecasts, and order requirements. Scheduling tools optimize production schedules for enhanced resource utilization.
- Inventory Management
- Efficient tracking and management of raw materials, work-in-progress (WIP), and finished goods. Real-time inventory data ensures optimal stock levels and prevents shortages or overstock situations.
- Bill of Materials (BOM) Management
- Centralized management of product structures, ensuring accurate and up-to-date BOM information. This feature is critical for maintaining consistency and traceability in manufacturing processes.
- Quality Control Integration
- Integration with quality control processes to monitor and enforce stringent quality standards at every stage of production. This ensures that the final products meet or exceed predefined quality benchmarks.
- Supply Chain Management
- Seamless coordination with suppliers, optimizing procurement processes, and ensuring a reliable supply chain for necessary materials. Manufacturing ERP facilitates end-to-end visibility across the supply chain.
- Financial Management
- Inclusion of financial modules for managing budgets, costs, and financial transactions. This ensures accurate financial reporting and compliance with accounting standards.
- Shop Floor Control
- Monitoring and control of activities on the shop floor, including work orders, resource allocation, and progress tracking. Real-time shop floor data enhances decision-making and responsiveness.
- Real-time Data Analytics
- Utilization of data analytics tools to provide real-time insights into various aspects of manufacturing operations. This enables data-driven decision-making and continuous improvement.
- Scalability
- The ability to scale with the business, accommodating changes in production volume, product lines, or overall business growth. Scalable ERP systems can evolve with the evolving needs of manufacturing enterprises.
- Integration with CAD/CAM Systems
- Integration with Computer-Aided Design (CAD) and Computer-Aided Manufacturing (CAM) systems for seamless collaboration between design and production teams.
Significance of Manufacturing ERP Software
- End-to-End Integration
- Manufacturing ERP Software integrates diverse business functions, from production planning and inventory management to financials and supply chain, fostering a cohesive and efficient environment.
- Operational Efficiency
- Automation of routine tasks, streamlined processes, and real-time visibility lead to improved operational efficiency. This translates to reduced lead times and enhanced responsiveness to market demands.
- Cost Optimization
- By optimizing inventory levels, preventing production delays, and improving resource allocation, Manufacturing ERP Software contributes to overall cost optimization and improved profitability.
- Regulatory Compliance:
- Adherence to industry regulations and standards is facilitated by the features of Manufacturing ERP systems, ensuring compliance and reducing the risk of regulatory issues.
- Accurate Forecasting
- Manufacturing ERP Software utilizes historical and real-time data to enhance the accuracy of demand forecasting. This assists businesses in aligning production plans with actual market demand.
- Quality Assurance
- Integration with quality control processes ensures that products meet or exceed predefined quality standards. This fosters customer satisfaction and helps build a reputation for quality.
- Visibility Across the Supply Chain
- Enhanced visibility into the entire supply chain, from procurement to production to distribution. This minimizes the risk of disruptions and improves overall supply chain efficiency.
- Strategic Decision-Making
- Real-time data analytics empower decision-makers with the information needed to make informed and strategic decisions. This agility is crucial in responding to changing market conditions.
Popular Manufacturing ERP Software Solutions
The realm of Manufacturing ERP (Enterprise Resource Planning) software is populated by various solutions, each tailored to meet the unique needs of manufacturing industries. Here are some popular Manufacturing ERP software solutions known for their robust features and industry-specific functionalities:
- SAP ERP
- Key Features: Comprehensive ERP solution covering various business functions, including manufacturing.
- Benefits: End-to-end integration, scalability, and support for complex manufacturing processes.
- Oracle NetSuite
- Key Features: Cloud-based ERP with manufacturing modules, offering flexibility and scalability.
- Benefits: Real-time visibility, streamlined operations, and integrated financials.
- Epicor ERP
- Key Features: Industry-specific manufacturing solutions tailored for various sectors.
- Benefits: Robust functionality, scalability, and support for global operations.
- IQMS Manufacturing ERP (now part of Dassault Systèmes)
- Key Features: Comprehensive ERP for manufacturing with an emphasis on real-time visibility.
- Benefits: End-to-end solution, integrated quality management, and support for complex supply chains.
- Microsoft Dynamics 365 for Finance and Operations
- Key Features: ERP system with manufacturing capabilities, seamlessly integrated with other Microsoft 365 applications.
- Benefits: Familiar Microsoft interface, flexibility, and scalability.
- PLEX Systems
- Key Features: Cloud-based manufacturing execution system (MES) providing real-time insights.
- Benefits: Scalability, visibility into the entire manufacturing process, and support for Industry 4.0 initiatives.
- SYSPRO ERP
- Key Features: Scalable ERP solution with modules for manufacturing and distribution.
- Benefits: Customizable, industry-specific functionality, and strong support for business growth.
- Infor CloudSuite Industrial (SyteLine)
- Key Features: Industry-specific ERP with a focus on manufacturing and distribution.
- Benefits: Flexible deployment options, comprehensive features, and scalability.
- Fishbowl Manufacturing
- Key Features: Manufacturing and inventory management software integrated with QuickBooks.
- Benefits: Quick implementation, seamless integration with QuickBooks, and affordability for small to mid-sized businesses.
- JobBOSS
- Key Features: Job shop and manufacturing process management solution.
- Benefits: Tailored for job shops, job costing, and production scheduling.
These Manufacturing ERP software solutions cater to various manufacturing industries, including discrete manufacturing, process manufacturing, and job shops. The choice of the right software depends on the specific needs, size, and complexity of the business operations. Before selecting a solution, businesses should thoroughly assess their requirements, consider scalability, and evaluate the level of support and training offered by the software provider. Additionally, exploring user reviews and seeking recommendations from industry peers can provide valuable insights into the performance and suitability of these software solutions for specific manufacturing environments.
Challenges of Implementing Manufacturing ERP Software:
- Implementation Costs
- The initial investment in implementing Manufacturing ERP Software, including software licenses, training, and infrastructure, can be substantial.
- Integration Complexity
- Integrating ERP software with existing systems or other software can be complex and may require careful planning.
- Employee Training
- Employees may face a learning curve when adapting to new ERP systems, impacting productivity during the transition period.
- Customization Challenges
- Customizing ERP software to fit specific business processes can be complex and may require additional resources.
- Data Migration Risks
- Migrating existing data to the new ERP system carries the risk of errors and requires meticulous planning.
- Resistance to Change
- Employees may resist changes to established workflows, potentially hindering successful adoption of the new system.
Choosing the Right Manufacturing ERP Software
Selecting the right Manufacturing ERP Software is a critical decision that requires a thorough understanding of business needs, scalability requirements, and industry-specific functionalities. Consider the following steps in the selection process:
- Assess Business Needs
- Identify the specific needs and pain points of your manufacturing operation. Consider factors such as production complexity, industry regulations, and scalability requirements.
- Evaluate Features
- Evaluate the features and functionalities offered by different ERP solutions. Ensure that the software aligns with your business processes and can support future growth.
- Consider Scalability
- Choose a Manufacturing ERP solution that can scale with your business. Ensure that it accommodates changes in production volume, new product lines, and overall business expansion.
- Integration Capabilities
- Assess the integration capabilities of the ERP software. Ensure that it can seamlessly integrate with existing systems and any other software used in your business.
- Vendor Reputation
- Research the reputation and track record of ERP software vendors. Choose a vendor with a history of successful implementations and ongoing support.
- User-Friendly Interface
- Consider the user-friendliness of the ERP system. An intuitive interface contributes to faster adoption and reduces the learning curve for employees.
- Industry-Specific Functionality
- If your manufacturing operation has industry-specific requirements, prioritize solutions that offer specialized functionalities catering to your industry.
- Cloud vs. On-Premises
- Decide whether a cloud-based or on-premises ERP solution is more suitable for your business. Cloud solutions offer flexibility, while on-premises solutions provide greater control over data.
- Trial or Demo
- Request a trial or demo of the ERP software to experience its features firsthand. This allows you to assess its usability and suitability for your manufacturing environment.
- Total Cost of Ownership (TCO)
- Consider the total cost of ownership, including not only licensing fees but also implementation costs, training, ongoing support, and any potential hidden costs.
- References and Reviews
- Seek references from businesses in your industry that have implemented the ERP software. Read reviews and testimonials to gain insights into the user experience.
Implementing Manufacturing ERP Software
- Planning
- Develop a comprehensive implementation plan outlining milestones, timelines, and responsibilities. Engage key stakeholders in the planning process.
- Data Migration
- Plan and execute data migration carefully to ensure the accuracy and integrity of existing data when transitioning to the new ERP system.
- Employee Training
- Provide thorough training to employees on using the new ERP system. Address any concerns and encourage a positive attitude towards the change.
- Pilot Implementation
- Consider a pilot implementation in a specific department or area before rolling out the ERP system organization-wide. This allows for fine-tuning and addressing any unforeseen issues.
- Continuous Improvement
- Embrace a culture of continuous improvement. Regularly review the performance of the ERP system and identify opportunities for optimization.
- Ongoing Support
- Ensure that there is a robust support mechanism in place for ongoing assistance. This includes addressing user queries, resolving issues, and providing updates.
Conclusion: The Future of Manufacturing Excellence
Manufacturing ERP Software stands at the forefront of digital transformation, empowering businesses to navigate the complexities of modern manufacturing with precision and agility. Its role extends beyond mere process optimization; it becomes a catalyst for innovation, data-driven decision-making, and sustainable growth.
As the manufacturing landscape continues to evolve, embracing advanced technologies such as Artificial Intelligence (AI), the Internet of Things (IoT), and predictive analytics, ERP systems are poised to evolve as well. The future promises a seamless integration of smart technologies within ERP frameworks, enabling manufacturers to embark on the journey of Industry 4.0.
In conclusion, the adoption of Manufacturing ERP Software is not just a technological upgrade; it’s a strategic investment in the future of manufacturing excellence. With the right ERP solution in place, businesses can transcend operational challenges, unlock new levels of efficiency, and embark on a trajectory of sustained success in the ever-evolving world of manufacturing.