In the ever-evolving landscape of modern manufacturing, staying competitive requires not just efficiency but a keen embrace of technological advancements. Manufacturing software emerges as a powerful ally, serving as the digital backbone that propels industries toward enhanced productivity, streamlined processes, and unparalleled control over production operations. This article delves into the realm of manufacturing software, unraveling its significance, key features, and the transformative impact it can bring to the manufacturing sector.
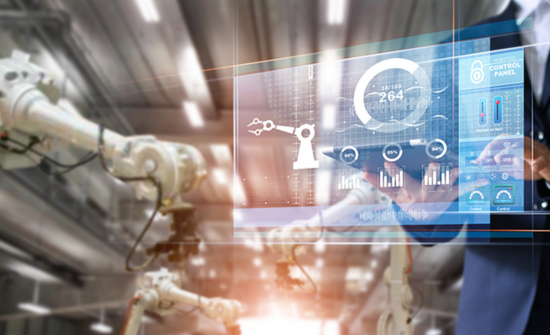
Understanding Manufacturing Software
Manufacturing software is a category of specialized solutions designed to streamline and optimize the various processes involved in production. From planning and scheduling to inventory management and quality control, these software systems are tailored to meet the unique needs of manufacturing industries. The overarching goal is to enhance operational efficiency, reduce costs, and provide real-time visibility into the entire production lifecycle.
Key Features of Manufacturing Software
- Production Planning and Scheduling:
- Manufacturing software facilitates the creation of detailed production plans, taking into account factors like resource availability, demand forecasts, and order requirements.
- Inventory Management:
- Efficient tracking and management of raw materials, work-in-progress (WIP), and finished goods to prevent shortages, overstock situations, and minimize carrying costs.
- Bill of Materials (BOM) Management:
- Centralized management of product structures, ensuring accurate and up-to-date BOM information for smooth production processes.
- Quality Control Integration:
- Integration with quality control processes to monitor and ensure adherence to stringent quality standards at every stage of production.
- Supply Chain Management:
- Seamless coordination with suppliers, optimizing procurement processes, and ensuring a reliable supply chain for necessary materials.
- Real-time Data Analytics:
- Providing actionable insights through real-time analytics, enabling data-driven decision-making and continuous improvement.
- Shop Floor Control:
- Monitoring and control of activities on the shop floor, including work orders, resource allocation, and progress tracking.
- Scalability:
- Ability to scale with the business, accommodating changes in production volume, product lines, or overall business growth.
- Integration with ERP Systems:
- Seamless integration with Enterprise Resource Planning (ERP) systems to unify manufacturing processes with other business functions.
- Mobile Accessibility:
- Access to critical manufacturing data and functionalities through mobile devices, fostering flexibility and real-time responsiveness.
Significance of Manufacturing Software
- Enhanced Efficiency
- Manufacturing software streamlines processes, reduces manual errors, and enhances overall operational efficiency.
- Cost Reduction
- By optimizing inventory levels, minimizing downtime, and improving resource allocation, manufacturing software contributes to cost reduction.
- Improved Productivity
- Automated workflows, real-time monitoring, and predictive analytics lead to increased productivity on the shop floor.
- Quality Assurance
- Integration with quality control processes ensures that products meet or exceed predefined quality standards.
- Agile Decision-Making
- Real-time data and analytics empower decision-makers with the information needed to respond quickly to changing conditions or market demands.
- Compliance and Traceability
- Manufacturing software helps maintain compliance with industry regulations and provides traceability of products throughout the production process.
- Customer Satisfaction
- Timely deliveries, consistent quality, and efficient processes contribute to heightened customer satisfaction.
- Adaptability to Changes
- Manufacturing software is designed to adapt to changes in demand, production requirements, and market conditions, providing businesses with flexibility.
Manufacturing software brings a multitude of advantages to business management, helping streamline operations, enhance efficiency, and provide better control over various aspects of the manufacturing process. However, like any technology, it comes with its set of challenges. Here’s a comprehensive look at the advantages and disadvantages of manufacturing software in business management:
Advantages of Manufacturing Software
- Efficiency Improvement
- Advantage: Automation of routine tasks and streamlined processes lead to increased overall efficiency in manufacturing operations.
- Real-time Visibility
- Advantage: Manufacturing software provides real-time insights into the production process, allowing for better decision-making and responsiveness to changes.
- Inventory Optimization
- Advantage: Effective inventory management reduces carrying costs, prevents stockouts, and ensures the availability of materials when needed.
- Production Planning and Scheduling
- Advantage: Advanced planning and scheduling capabilities help optimize production schedules, leading to improved resource utilization.
- Quality Control Integration
- Advantage: Integration with quality control processes ensures adherence to quality standards and reduces the likelihood of defects.
- Cost Reduction
- Advantage: Optimizing resource usage, reducing waste, and preventing overstock situations contribute to overall cost reduction.
- Enhanced Communication
- Advantage: Manufacturing software facilitates communication and collaboration between different departments, fostering a more cohesive work environment.
- Accurate Reporting
- Advantage: Automated reporting features provide accurate and up-to-date information, supporting data-driven decision-making.
- Supply Chain Management
- Advantage: Improved coordination with suppliers and better supply chain visibility contribute to a more reliable and efficient procurement process.
- Scalability
- Advantage: Manufacturing software is often scalable, accommodating the growth and changing needs of a business.
Disadvantages of Manufacturing Software
- Implementation Costs
- Disadvantage: The initial costs associated with implementing manufacturing software, including licensing, training, and infrastructure, can be significant.
- Learning Curve
- Disadvantage: Employees may face a learning curve when adapting to new software, potentially impacting productivity during the transition period.
- Customization Challenges
- Disadvantage: Customizing manufacturing software to fit specific business processes can be complex and may require additional resources.
- Integration Issues
- Disadvantage: Integrating manufacturing software with existing systems or other software can be challenging and may lead to disruptions.
- Data Security Concerns
- Disadvantage: Storing sensitive business data in manufacturing software poses potential security risks, requiring robust cybersecurity measures.
- Maintenance and Updates
- Disadvantage: Regular maintenance and updates are necessary to keep the software functioning optimally, adding to ongoing costs.
- Resistance to Change
- Disadvantage: Employees may resist changes to established workflows, potentially hindering successful adoption of the software.
- Dependence on Data Accuracy
- Disadvantage: Manufacturing software heavily relies on accurate data; any discrepancies can lead to errors in production planning and resource allocation.
- Scalability Limitations
- Disadvantage: Some manufacturing software solutions may face challenges in scaling up to accommodate larger enterprises or significant changes in production volume.
- Continuous Training Needs
- Disadvantage: Ongoing training and support may be required to keep users updated on new features or changes in the software.
In conclusion, while manufacturing software provides substantial benefits in terms of efficiency and control, businesses need to carefully evaluate their specific needs and challenges before implementation. The advantages often outweigh the disadvantages in the long run, but successful adoption requires thorough planning, effective training, and ongoing commitment to addressing potential challenges.
Popular Manufacturing Software Solutions
Manufacturing software plays a pivotal role in streamlining operations, enhancing efficiency, and providing real-time insights for businesses in the manufacturing sector. Here are some popular manufacturing software solutions known for their robust features and industry-specific functionalities:
- SAP ERP
- Key Features: Comprehensive ERP solution covering various business functions, including manufacturing.
- Benefits: End-to-end integration, scalability, and support for complex manufacturing processes.
- Oracle NetSuite
- Key Features: Cloud-based ERP with manufacturing modules, offering flexibility and scalability.
- Benefits: Real-time visibility, streamlined operations, and integrated financials.
- Epicor ERP
- Key Features: Industry-specific solutions tailored for manufacturing and distribution.
- Benefits: Robust functionality, scalability, and support for global operations.
- IQMS Manufacturing ERP (now part of Dassault Systèmes)
- Key Features: Comprehensive ERP for manufacturing with an emphasis on real-time visibility.
- Benefits: End-to-end solution, integrated quality management, and support for complex supply chains.
- Microsoft Dynamics 365 for Finance and Operations
- Key Features: ERP system with manufacturing capabilities, seamlessly integrated with other Microsoft 365 applications.
- Benefits: Familiar Microsoft interface, flexibility, and scalability.
- PLEX Systems
- Key Features: Cloud-based manufacturing execution system (MES) providing real-time insights.
- Benefits: Scalability, visibility into the entire manufacturing process, and support for Industry 4.0 initiatives.
- SYSPRO ERP
- Key Features: Scalable ERP solution with modules for manufacturing and distribution.
- Benefits: Customizable, industry-specific functionality, and strong support for business growth.
- Fishbowl Manufacturing
- Key Features: Manufacturing and inventory management software integrated with QuickBooks.
- Benefits: Quick implementation, seamless integration with QuickBooks, and affordable for small to mid-sized businesses.
- JobBOSS
- Key Features: Job shop and manufacturing process management solution.
- Benefits: Tailored for job shops, job costing, and production scheduling.
- Global Shop Solutions
- Key Features: ERP software designed for small and medium-sized manufacturers.
- Benefits: Simplified manufacturing management, comprehensive features, and ease of use.
These software solutions cater to various manufacturing industries, including discrete manufacturing, process manufacturing, and job shops. The choice of the right manufacturing software depends on the specific needs, size, and complexity of the business operations. Before selecting a solution, businesses should thoroughly assess their requirements, consider scalability, and evaluate the level of support and training offered by the software provider. Additionally, exploring user reviews and seeking recommendations from industry peers can provide valuable insights into the performance and suitability of these software solutions for specific manufacturing environments.
How To Subscribe Manufacturing Software
Subscribing to manufacturing software typically involves a series of steps, and the process may vary depending on the specific software provider. Here’s a general guide on how you can subscribe to manufacturing software:
- Research and Choose a Software:
- Before subscribing, thoroughly research different manufacturing software options available in the market. Consider your business requirements, the size of your operation, scalability needs, and any industry-specific features. Once you’ve identified a suitable software solution, proceed to the next steps.
- Contact the Software Provider:
- Visit the official website of the manufacturing software provider or contact their sales team. Most providers have a dedicated sales department that can provide information on pricing, features, and subscription plans.
- Request a Demo:
- Many software providers offer demonstrations or free trials to allow potential users to explore the software’s features and functionalities. Request a demo or take advantage of a trial period to ensure that the software meets your business needs.
- Discuss Pricing and Subscription Plans:
- Engage in discussions with the software provider’s sales team to understand the pricing structure and available subscription plans. Manufacturing software often involves monthly or annual subscription fees based on factors such as the number of users, features included, and the size of the business.
- Customization and Integration:
- If customization or integration with other systems is required for your specific business processes, discuss these needs with the software provider. Ensure that the software can be tailored to fit seamlessly into your manufacturing workflow.
- Negotiate Terms and Conditions:
- Once you are satisfied with the proposed subscription plan and pricing, discuss the terms and conditions of the subscription agreement. Pay attention to factors such as contract duration, renewal terms, and any potential additional costs.
- Confirm Support and Training Options:
- Inquire about the support and training options provided by the software vendor. Understand the level of support available, response times for assistance, and any additional costs associated with support services.
- Review the Subscription Agreement:
- Carefully review the subscription agreement and terms before committing. Pay attention to any clauses related to cancellation, data ownership, and service level agreements (SLAs).
- Provide Necessary Information:
- The software provider may require certain information to set up your subscription, such as the number of users, business details, and payment information. Provide accurate and necessary details to facilitate a smooth onboarding process.
- Complete the Subscription Process:
- Once all details are finalized and terms are agreed upon, proceed to complete the subscription process. This may involve signing a contract, making the initial payment, and gaining access to the software.
- Onboarding and Training:
- Take advantage of any onboarding or training sessions offered by the software provider. Ensure that your team is familiar with the software’s features and functionalities to maximize its benefits.
- Regularly Review and Optimize:
- Periodically review your usage of the manufacturing software, its impact on operations, and the level of support received. Optimize your usage based on evolving business needs.
Remember that the process may vary, and it’s essential to communicate openly with the software provider throughout the subscription process. Additionally, ensure that you have a clear understanding of the software’s capabilities, support mechanisms, and any ongoing costs associated with the subscription.
Choosing the Right Manufacturing Software
Selecting the most suitable manufacturing software involves a careful consideration of the specific needs and goals of the business. Factors such as the size of the operation, industry requirements, scalability, and integration capabilities should guide the decision-making process. Additionally, a robust implementation plan and adequate training for users are essential for maximizing the benefits of manufacturing software.
In conclusion, manufacturing software stands as a linchpin in the modernization and evolution of the manufacturing sector. Its transformative impact extends beyond the shop floor, influencing overall business operations and positioning industries for success in the digital era. As manufacturing continues to advance, the adoption of sophisticated software solutions becomes not just a choice but a strategic imperative for businesses aiming to thrive in the competitive landscape.